What is Porosity in Welding: Understanding Its Reasons and Enhancing Your Skills
What is Porosity in Welding: Understanding Its Reasons and Enhancing Your Skills
Blog Article
Porosity in Welding: Identifying Common Issues and Implementing Best Practices for Avoidance
Porosity in welding is a prevalent concern that usually goes undetected till it triggers substantial problems with the stability of welds. In this conversation, we will certainly discover the vital variables adding to porosity formation, examine its destructive impacts on weld performance, and discuss the ideal practices that can be taken on to reduce porosity incident in welding procedures.
Usual Reasons For Porosity
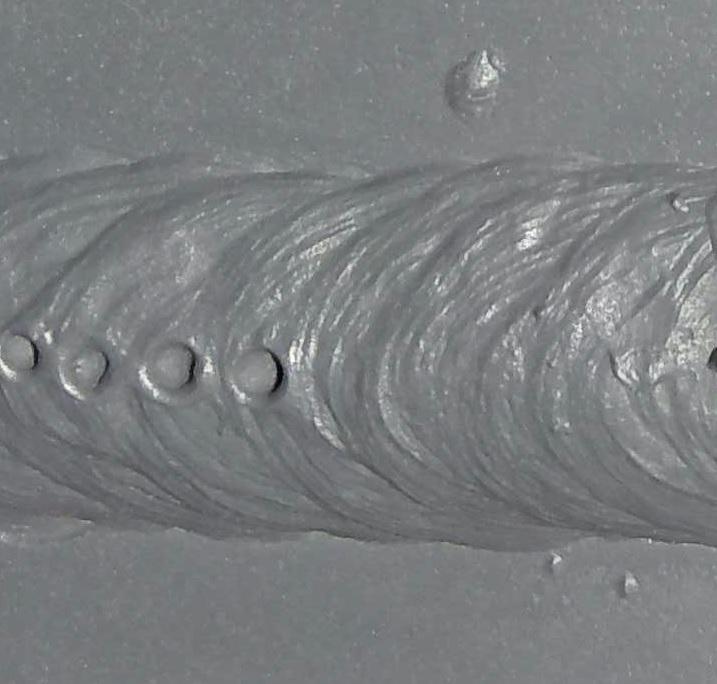
An additional constant culprit behind porosity is the presence of pollutants externally of the base steel, such as oil, grease, or rust. When these pollutants are not efficiently eliminated before welding, they can evaporate and come to be trapped in the weld, causing defects. In addition, utilizing dirty or wet filler products can present contaminations into the weld, adding to porosity issues. To reduce these common sources of porosity, thorough cleaning of base steels, appropriate securing gas selection, and adherence to optimal welding parameters are necessary methods in attaining high-quality, porosity-free welds.
Influence of Porosity on Weld High Quality

The existence of porosity in welding can substantially endanger the structural honesty and mechanical buildings of welded joints. Porosity creates gaps within the weld metal, damaging its overall stamina and load-bearing capacity.
Welds with high porosity levels tend to display lower influence strength and lowered ability to flaw plastically before fracturing. Porosity can impede the weld's capability to properly transmit pressures, leading to premature weld failure and possible safety and security dangers in critical structures.
Ideal Practices for Porosity Prevention
To enhance the architectural integrity and top quality of bonded joints, what particular actions can be carried out to reduce the incident of porosity during the welding procedure? Porosity avoidance in welding is vital to make certain the stability and toughness of the last weld. One reliable technique is correct cleansing of the base steel, removing any type of contaminants such as corrosion, oil, paint, or dampness that could cause gas entrapment. Making sure that the welding equipment is in good problem, with tidy consumables and proper gas circulation rates, can also dramatically reduce porosity. Additionally, maintaining a secure arc and managing the welding parameters, such as voltage, existing, and take a trip speed, helps produce a consistent weld pool that lessens the danger of gas entrapment. Using the proper welding method for the particular material being bonded, such as readjusting the welding angle and weapon setting, can better avoid porosity. Normal evaluation of welds and immediate removal of any type of issues identified during the welding process are important methods to stop porosity and generate high-quality welds.
Value of Correct Welding Strategies
Executing appropriate welding dig this strategies is vital in making certain the structural integrity and high quality of welded joints, developing upon the foundation of reliable porosity prevention procedures. Extreme heat read review can lead to raised porosity due to the entrapment of gases in the weld swimming pool. In addition, making use of the proper welding specifications, such as voltage, current, and travel rate, is vital for achieving audio welds with minimal porosity.
Furthermore, the selection of welding process, whether it be MIG, TIG, or stick welding, should align with the details requirements of the task to ensure optimum results. Appropriate cleansing and prep work of the base metal, in addition to selecting the ideal filler material, are likewise essential parts of proficient welding methods. By sticking to these best practices, welders can decrease the threat of porosity development and produce high-quality, structurally audio welds.
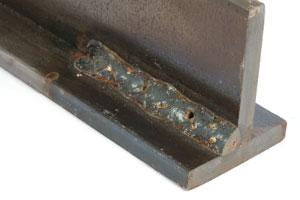
Checking and High Quality Control Steps
Quality assurance actions play a vital duty in confirming the stability and dependability of welded joints. Recommended Site Checking procedures are vital to find and protect against porosity in welding, guaranteeing the strength and toughness of the last item. Non-destructive screening approaches such as ultrasonic screening, radiographic screening, and visual evaluation are typically utilized to recognize prospective flaws like porosity. These strategies permit the analysis of weld quality without compromising the stability of the joint. What is Porosity.
Conducting pre-weld and post-weld evaluations is also important in keeping quality assurance standards. Pre-weld examinations include validating the materials, tools setups, and cleanliness of the workplace to stop contamination. Post-weld examinations, on the various other hand, assess the last weld for any flaws, including porosity, and validate that it meets specified criteria. Carrying out a thorough quality control strategy that consists of extensive testing treatments and evaluations is critical to decreasing porosity problems and guaranteeing the general top quality of welded joints.
Conclusion
In conclusion, porosity in welding can be a common issue that affects the quality of welds. By determining the common sources of porosity and implementing ideal practices for avoidance, such as proper welding strategies and testing steps, welders can make sure premium quality and trustworthy welds. It is necessary to prioritize avoidance techniques to reduce the event of porosity and keep the stability of bonded structures.
Report this page